COBRA INTERNATIONAL COMMISSION NEW PREPREG COMPRESSION MOULDING LINE
5th April 2021
Cobra International is pleased to announce the commissioning of a new prepreg compression moulding production line. Now complete, and with series production of parts underway, the new production capacity delivers prepreg carbon parts with a final surface finish straight from the mould tool.
Though COBRA has produced prepreg parts for several decades at its 100,000m2 manufacturing facility, most previous production has been via autoclave or vacuum bag processing. With COBRA’s strategy targeting higher volume applications, a faster production process was required. Developed during the second half of 2020, COBRA’s new compression moulding line is currently producing monolithic carbon fibre wing and mast components for leading foil brands Phantom Windsurfing and MFC.
The COBRA production engineering team has focussed on a full value stream mapping of the manufacturing process, optimising the Phantom IRIS X foil production for efficiency, reduced cycle time and to get the final part dimensions and surface finish straight from the mould.
COBRA has developed processes to analyze each new compression moulding part and produce a ply book of 2D shapes. Individual prepreg plies are stacked, preformed in low temperature tooling, and then loaded into steel mould tools for the final compression moulding cure cycle.
“There are three key aspects of our new compression moulding production that offer major benefits to our customers” comments Pierre Olivier Schnerb, CTO. “Firstly, we can offer customers extremely rapid prototyping, with full prepreg parts available within ten days. Our own ply book development process is a critical part of this rapid response, helping us to define a full ply book for each mould geometry in only a few hours. Lastly, we were clear from the outset that we had to remove the need for a traditional multi-layer clear coat. It was a challenge, but we now make highly structural parts with the required surface finish straight from the mould.”
COBRA continues to develop its prepreg compression moulding technology with resin matrix and mould heating improvements promising short cycle times in the future. Following the successful integration of the first compression moulding line at COBRA, the company is currently scaling up with a second line planned to come on stream in the second half of 2021. This additional capacity will support prepreg component production across a diverse range of applications such as foils, prosthetics, automotive and motorcycle components.
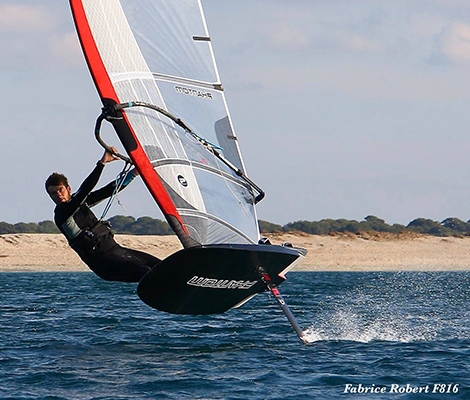